Step 1
Preparing your clay slabs
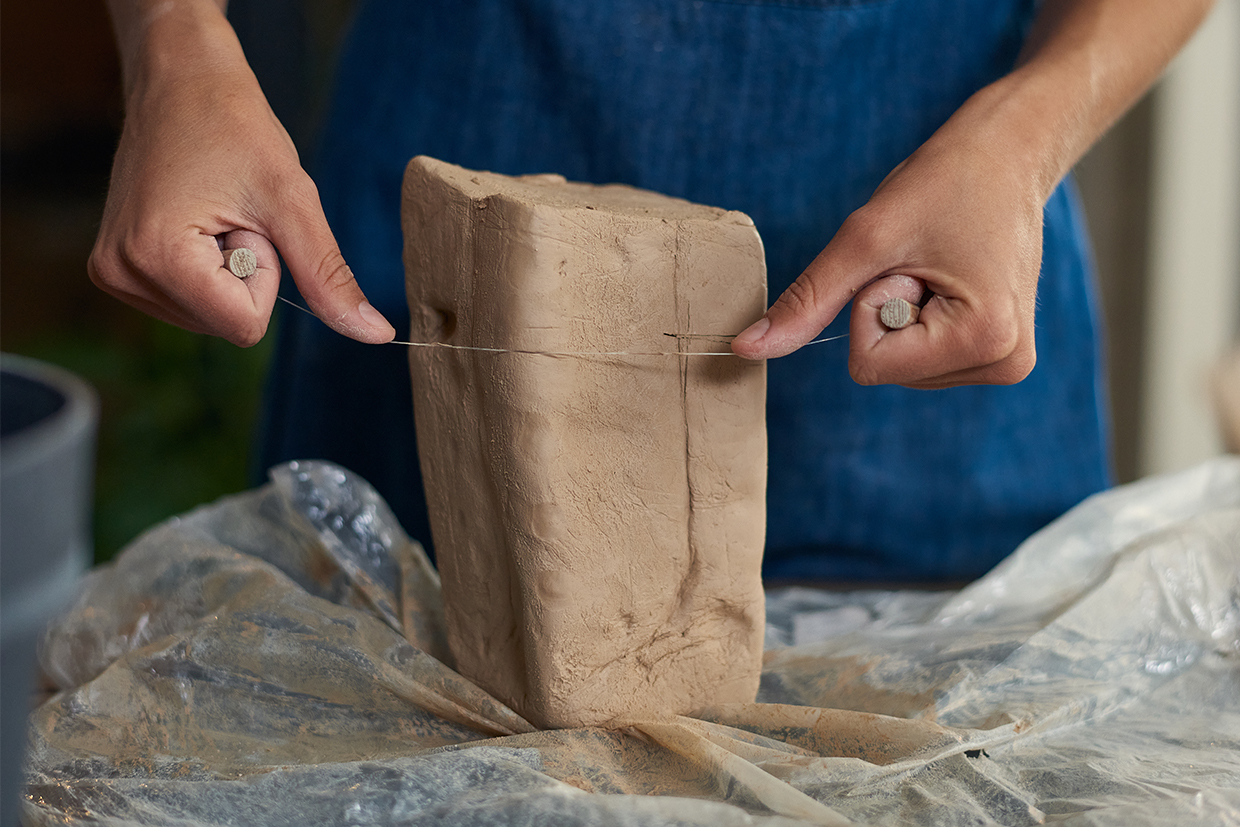
First things first, you need to take your block of clay and turn it into slabs. There are a few different ways of doing this, from using specific tools to flattening it by hand. We’ll briefly cover the different methods now, but whichever you choose the most important thing is to create an even slab that has a uniform thickness.
Slab roller machine
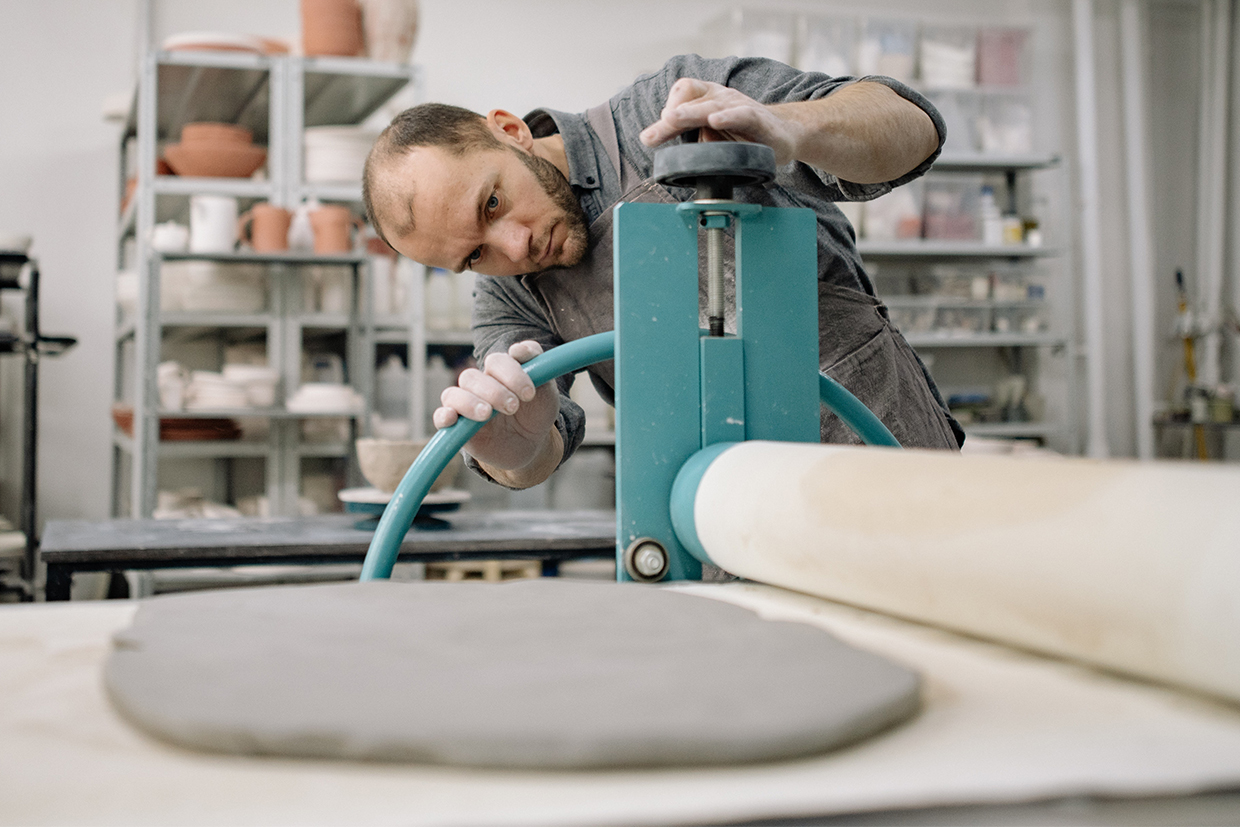
If you have access to a proper pottery studio, you can use a slab roller machine. These are large tabletop machines that squeeze the clay through rollers to create an even and flat sheet – a bit like a pasta maker or an old-fashioned laundry mangle! Alternatively, you can also use a bow harp clay slicer to cut a neat slab straight off your block of clay.
By hand with a rolling pin
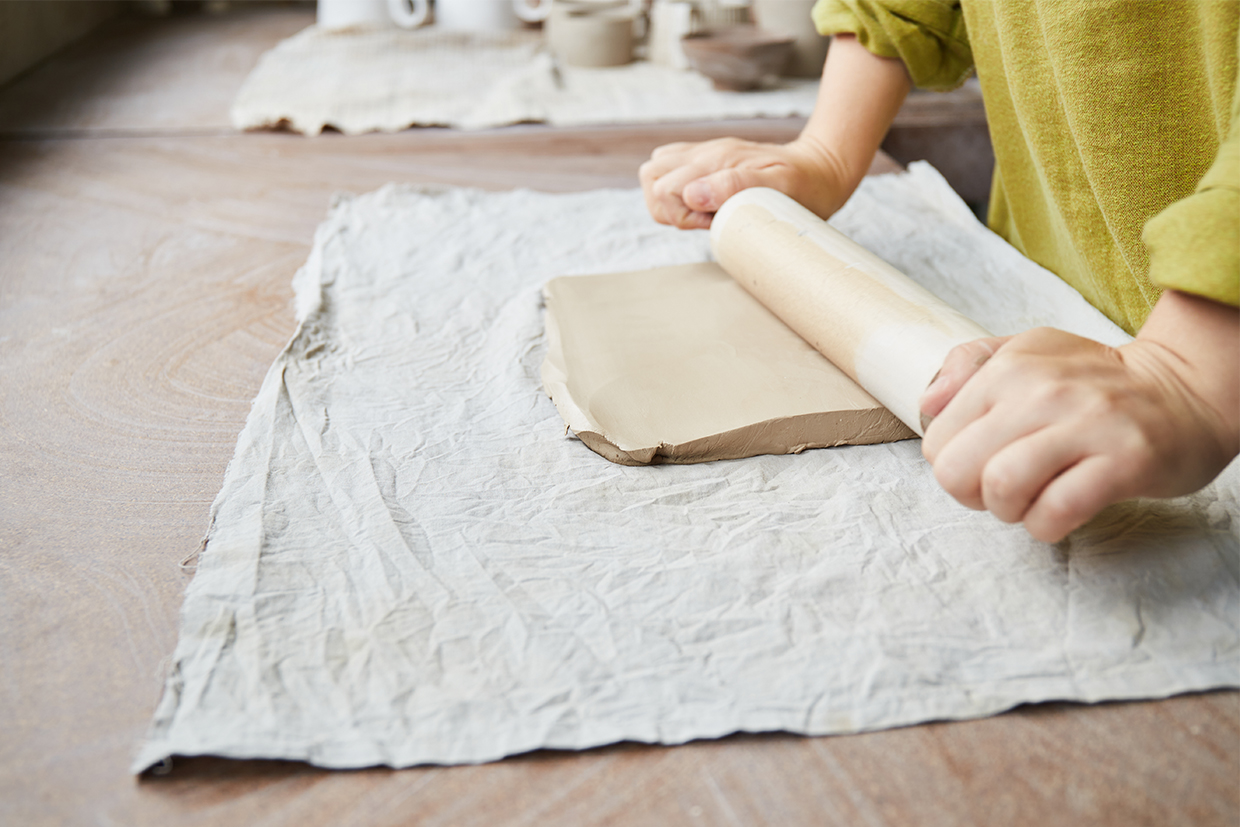
For those of you who like to get stuck in with your hands, a good old-fashioned rolling pin on a non-stick surface will also do the job.
By hand without a rolling pin
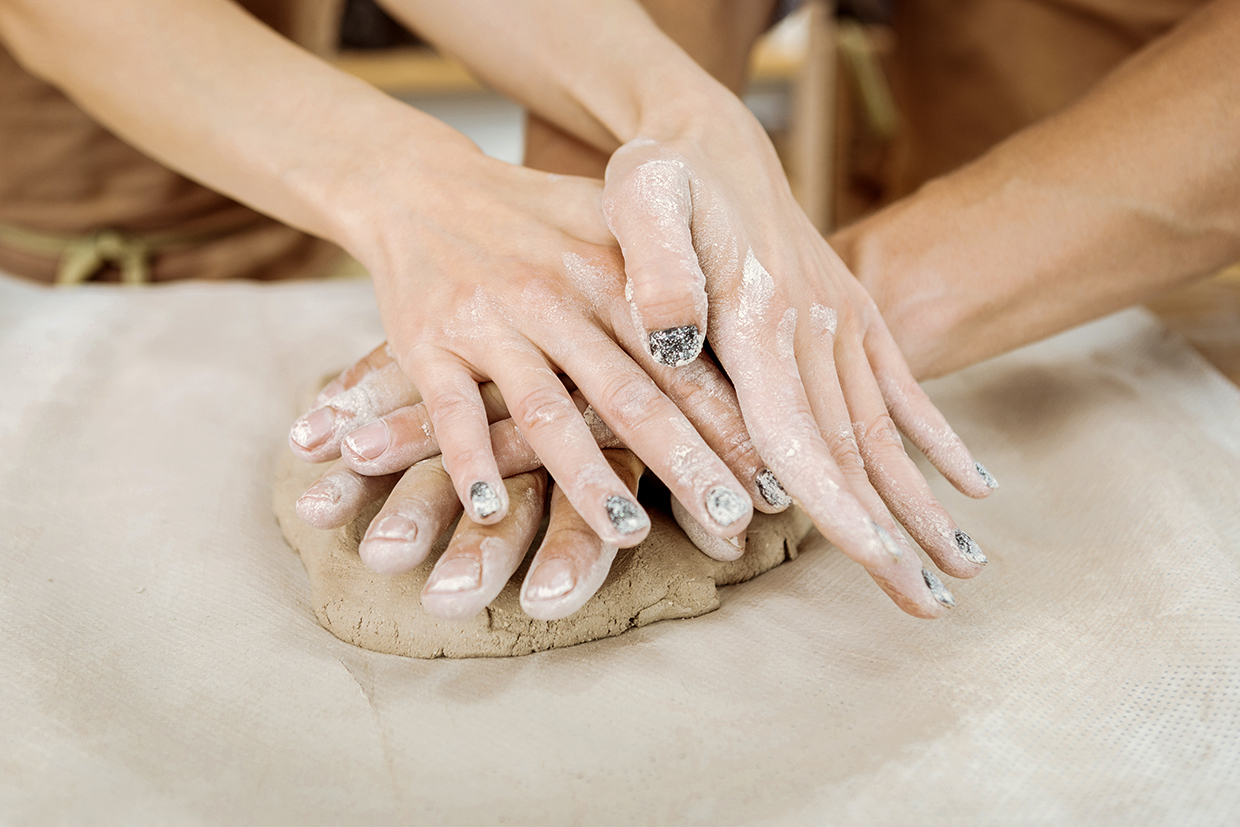
You can even just flatten by hand. Give your clay a good strong throw onto your surface at a slight angle, then repeat. Each time you slap the slab onto the surface it will stretch and get a bit flatter, keep going until you reach your desired thickness.
The thickness of your final slab will depend on the size of your project and what you hope to achieve. Realistically you will want your slab to be no thinner than a quarter of an inch, going up to half an inch for bigger projects or even in increments up to an inch thick for really big makes.
Step 2
Soft slab or dry slab?
Depending on the effect you hope to achieve with your slab, you now need to make the decision of whether you require a soft slab or a dry slab.
Soft slab

A soft slab is pretty much ready to go once you’ve flattened it and is best used when you want to fold or manipulate your slab into curves or angles. Because the clay is still pliable, you can easily add folds or arrange it into shapes.
However, it won’t be strong enough to fully support itself, so this technique works best when placed over a mould or support structure. Soft slabs are generally better for smaller builds, as larger slabs that are soft can still potentially stretch, warp, or even collapse.
Dry slab
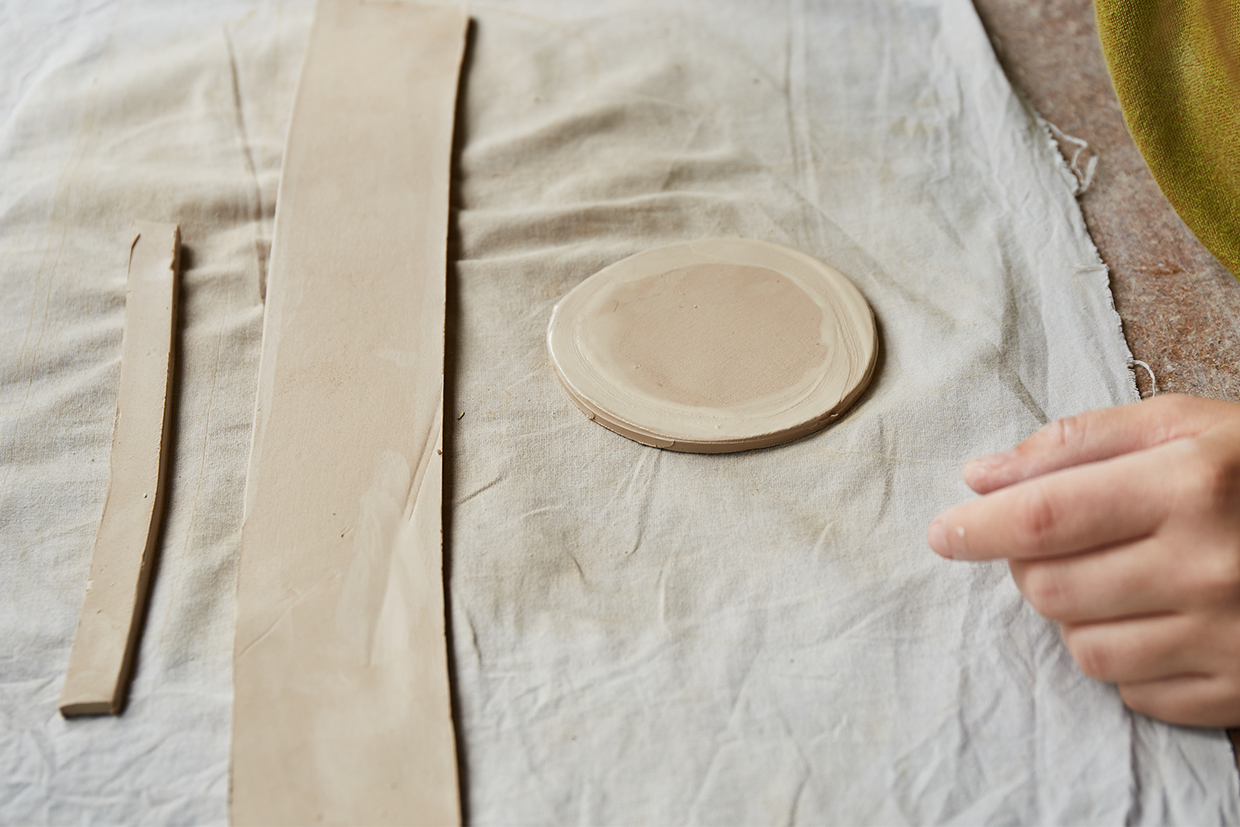
A dry slab is one that has been left to dry to a state that is described as ‘leather hard’. There are three stages of dryness your clay will need to go through before firing – the first when it’s still soft and pliable, the second when it’s leather hard, and finally when it’s bone dry.
The leather hard stage can take anywhere from one to three days depending on the atmosphere and environment. It’s worth checking on your slab regularly, as you want the clay to still be cool to the touch but not sticky. You should still be able to gently bend and manipulate your leather hard slab without it cracking, however, this will only get more difficult as the clay dries out further.
Dry slabs are much better suited to larger builds and are particularly useful for creating smooth and solid walls for geometric structures such as cuboids.
Step 3
Shape your slab
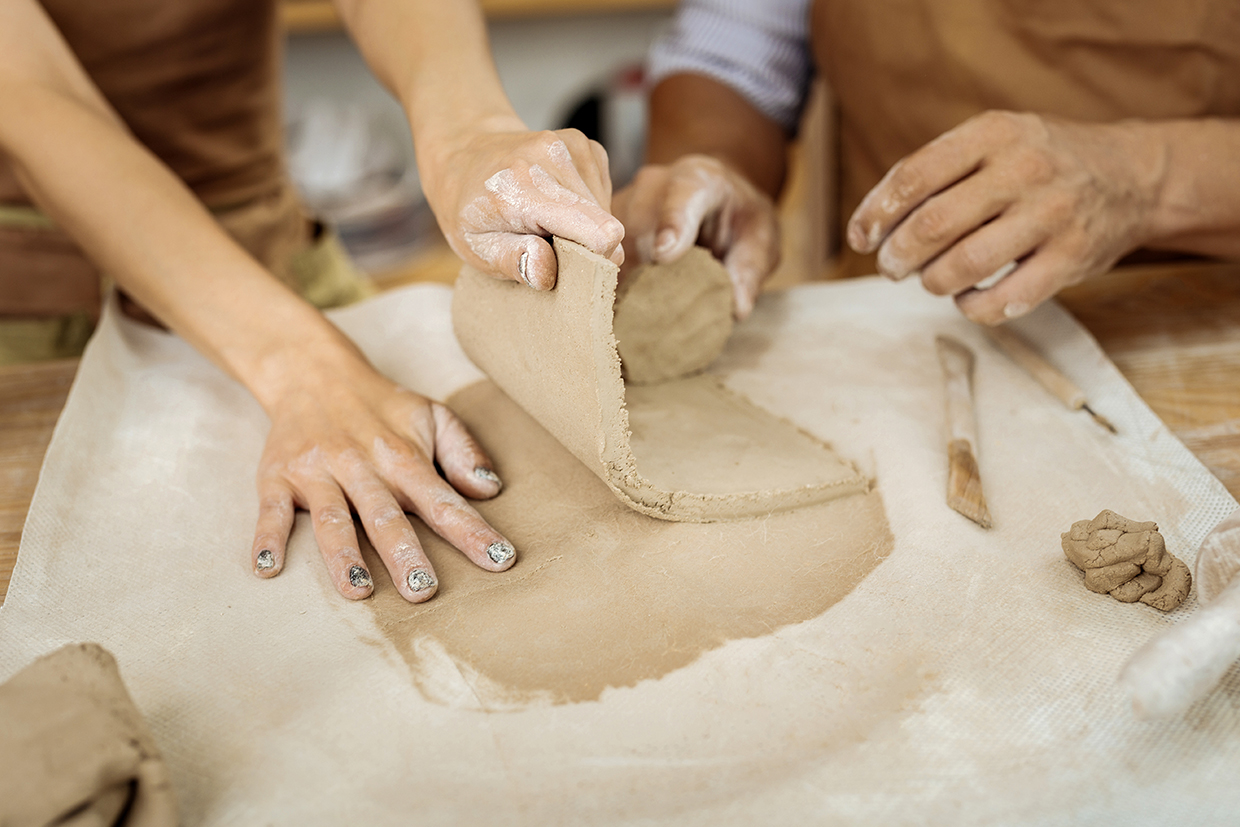
Once your slab is made and it has had the appropriate drying time, it’s time to shape your slab. If you haven’t done it already, now is a good time to cut your slab to desired measurements. You can still trim off any excess at any point during your clays leather hard stage.
With your slab now at the perfect size, it’s time to make your desired shape. Generally, this is best done by hand, although you can also use moulds or objects to help you. Take your time with your shaping, especially with dry slabs.
When using soft slabs, it’s wise to make sure you have a mould or support structures to help maintain your shapes while it dries to the leather hard stage. It may even be helpful to have someone act as an extra pair of hands if you’re making particularly large structures with soft slabs.
Step 4
Score and slip to join areas
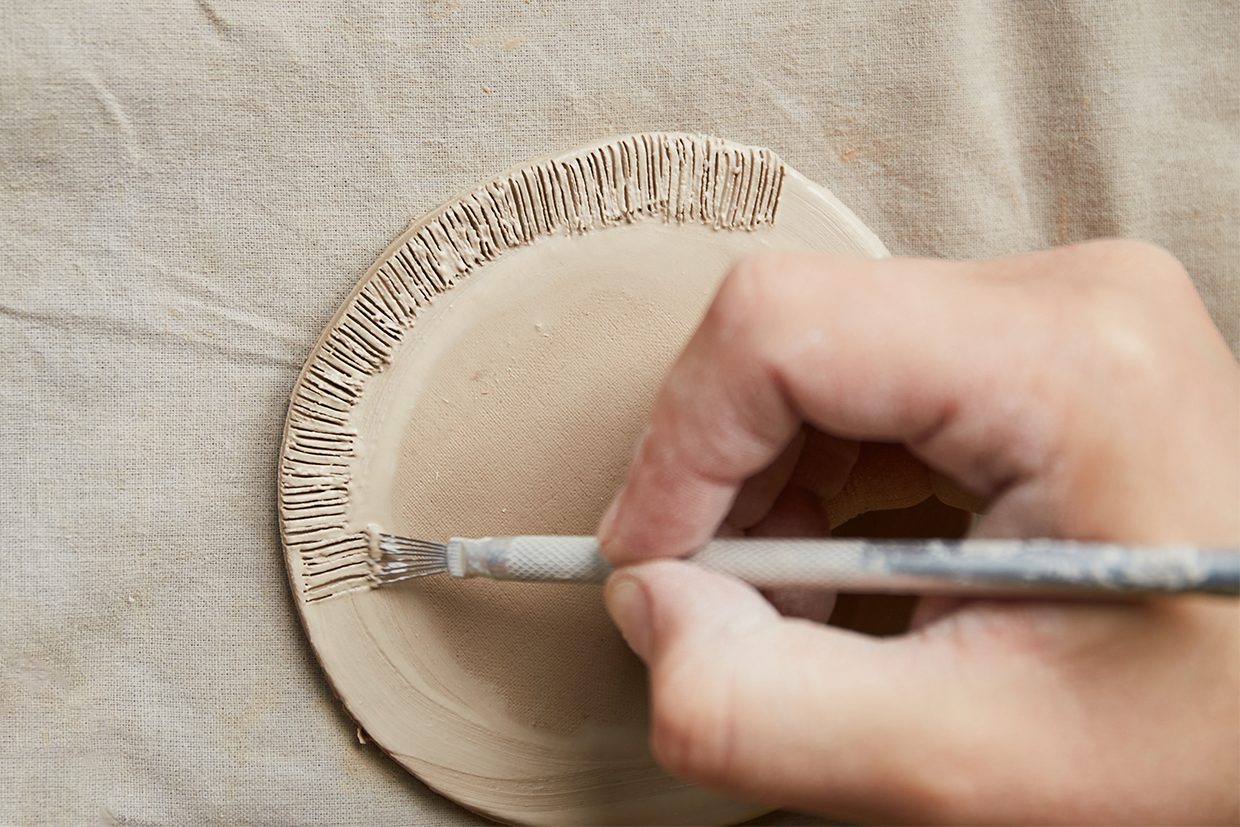
Regardless of whether you’re using a soft slab or a dry slab, both can be joined with the classic score and slip technique. This is the same method used in many types of pottery projects to create joins. If you’re using a soft slab it’s best to let it dry out a bit to get a better join.
All you need to do is scrape the areas you wish to join to with a modelling tool (or even something as simple as a fork). You’re looking to create a scratched texture which will help your two pieces grip together. Paint a bit of slip on top of the scoring and press your pieces together – hard enough to join them but not so hard that you squash the clay.

You may want to add a support to help your two pieces stay in the same position when joining, especially when they’re standing vertically. It’s worth keeping in mind that joins are often the likeliest areas to break in the kiln firing process, so it’s worth taking the time to ensure you get a really good connection and quality join.

Step 5
Dry and kiln fire
Once you’ve achieved your desired shape and done any required joins, you can smooth down any edges or seams and leave until bone dry. Then your piece is ready for firing in the kiln.
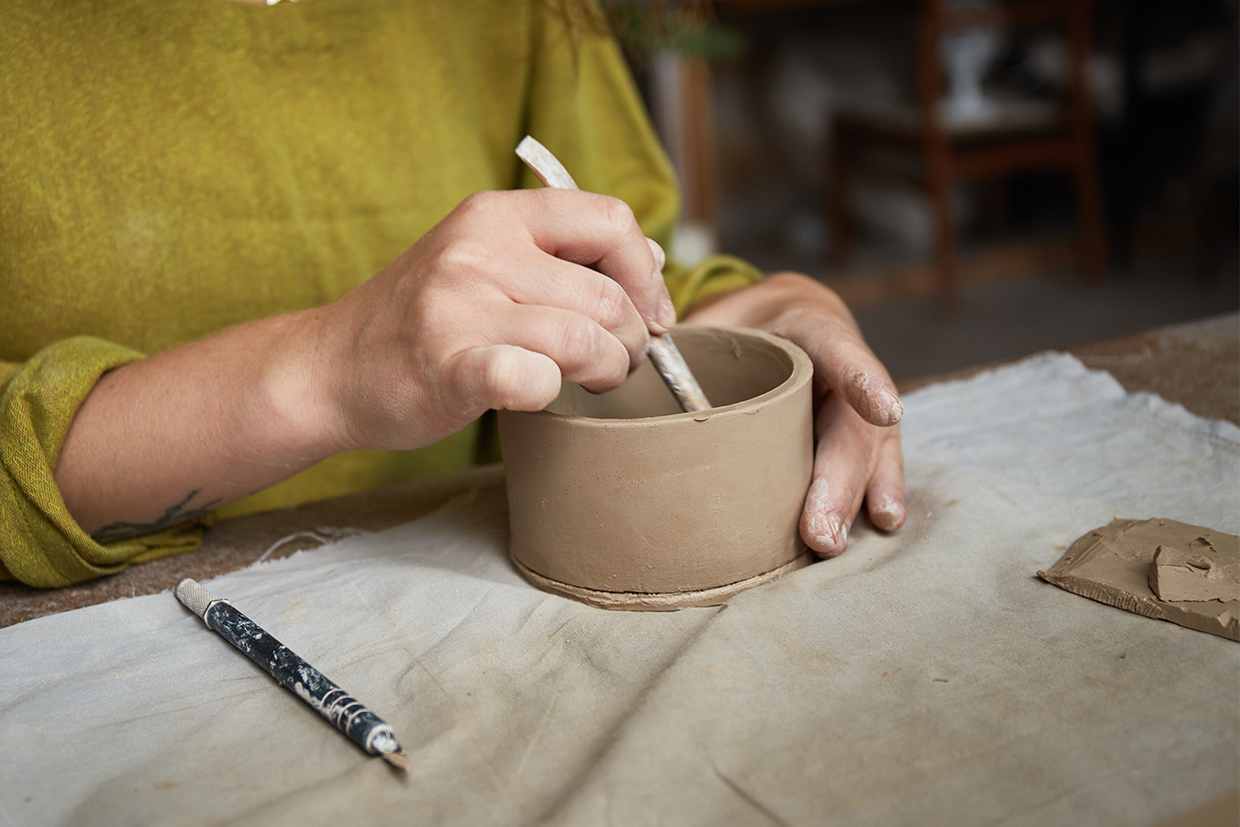